Why Practice Inventory Control?
Every company that is trying to get its grips around what they have talked about Inventory control. Companies that are trying to understand what they need to meet their demands are looking into Inventory Controls. The concept of Inventory Control is straightforward. Knowledge of what you have and what you can sell. Additional controls are used to make sure that this information is correct, accurate, and actionable.
From an accounting standpoint, Inventory controls are critical in understanding business costs. Goods sitting in inventory carry a cost. The labor required to put that item away in the warehouse and to count it periodically also carries a cost associated with it. Rarely recorded are equipment usage and resource execution. These operations have a cost related to them. To properly calculate the true cost of an item you need to capture all the resource, time, and equipment costs. Examples of this are tasks like picking, prepping, and item consumption (Manufacturing or sales). Capturing the associated wear on the equipment used is also necessary.
But, do we really need to practice inventory control? We’ll consume inventory as soon as we can. A rush order (at a premium cost) will resolve any stock-out situation. These simple thought processes may work for small operations, but as you grow, these processes can signal a growing company’s demise.
Business Requirements for Inventory Controls
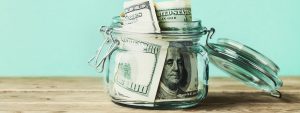
Inventory Contol verifies the on-hand value of assets
Inventory Control Practices meet the following business requirements:
- Accuracy of Inventory Valuation for Investors and Lien Holders
- Research and analysis of processes to push cost-saving initiatives
- Minimization of process downtime due to stock-outs
- Managers wanting visibility and understanding of their operations
- Workforce Management
Although all 5 reasons are valid, experience has shown that 80% of the time you will encounter the first two reasons as the impetus for the implementation of the processes. Executive management is looking for ways to improve the operations budget and the profit margins for their company. Inventory carrying costs are the second-highest number on their Balance sheet (Resource Overhead is the first). Major investors like venture capitalists and financial institutions will want to audit the Inventory on-hand reporting to make sure that the numbers are accurate and that there are not some misleading business practices in place. The stronger the inventory control system, the more accurate these numbers are and in turn the shorter the investor audits can last.
A company that is always “In Search of Excellence”[1] or steadfast in the beliefs of “Six Sigma”[2] will hold a manager to Key Performance Indicators (KPI’s) that are based around productivity and cost reduction. They will also want to make sure that their management personnel is “Champions of Change.” This is critical to the cause of improved practices or else the processes will remain stagnant and resistant to new philosophies and overall change. To learn more about this, please check out the Impact of Inventory Control Systems on your Supply chain.
Inventory Control: Why Carry Inventory?
In a perfect world, the material would be consumed onto a work order or into a process batch as soon as it is received onsite. Likewise, Finished Goods would be sold and shipped out to a customer as soon as the manufacturing operation is complete. These practices would optimize costs and reduce the need for having Inventory on-hand, however, this is rarely the reality.
Factors that contribute to the need to carry inventory and practice Inventory Control:
Manufacturing Operations and Material availability:
- Many manufacturers will run a 24/7 production schedule. (24 hours a day, 7 days a week)
- Materials will only arrive in the facility between 9am and 5pm, Monday through Friday.
- To meet the Inventory demand during the hours where materials are not actively arriving at the facility additional inventory must be stored.
Supply/Demand planning constraints with Inventory Control:
Cost Efficiency Constraints:
-
-
- The optimal profit margin requires more Raw Materials need to be purchased
- Finished Goods need to be produced at a specific pace to achieve the optimal piece rate or cost per item.
-
Build up Supply in anticipation of upcoming demand.
You have a sales order for a large number of goods. They must ship together on a specific date. To meet that demand, you must build up the supply over time.
For example, 6000 goods are ordered to be shipped in 6 months. The production rate is 250 widgets a week. To meet the demand, production needs to start 24 weeks before the shipment date. Each week of the 23 weeks leading up to the shipment date requires that additional inventory on-hand. (1 week of production subtracted from the shipment date)
Changes in Customer Demand
Changes in Customer demand may lead to an excess of supply. Customers will cancel or delay orders at any time. Manufacturing is already underway. It is cheaper to store the goods than to scrap them. The goods will be shipped once a new order is placed.
Changes to a manufacturing schedule:
Manufacturing equipment can go down unexpectedly and cause a break in the production plan. This may cause a change in manufacturing line runs and the need for materials to be consumed. During such a “downtime” another product line will get started instead. This is down to maximize resource efficiency. To perform ad hoc changes in production, excess raw materials will need to be on-hand. The produced goods will also need to be stored.
Conclusion – Why Practice Inventory Control?
As you begin to fully understand the needs to properly carry, track, and control inventory; your company’s capabilities will grow. Subsequently, the next step will be to add additional controls. For instance, Cycle Counts are an additional form of inventory control. A Warehouse Management (WMS) Solution is also the next progression. To get there, you will need to assess if you are ready. A simple checklist is available in my post 5 Questions to See If You are Prepared for a WMS Solution.
[1] “In search of Excellence” a Book by Robert H. Waterman Jr. and Tom Peters
[2] Six Sigma: https://www.isixsigma.com/new-to-six-sigma/getting-started/what-six-sigma/