Unlock the Power to optimize your WMS Solution
Congratulations, you have successfully answered the questions asked in 5 Questions to See If You are Prepared for a WMS Solution and a solution is in place. Time to sit back, reap the returns, and watch the increased productivity soar. Right? Or is it time to unlock the power to further optimize your solution?
There will always be new practices that can be utilized to further your solution. In this post, we will dive into six systems. These systems are focused on space, time, and resource utilization.
Advance Features and the Barriers to Achieve Results
As facilities strive to become more efficient and more advanced with their technology; a transformational change will affect the culture of the workforce. Below, we will go into each of the 6 advanced systems. What they are and their benefits and barriers to entry will be detailed.
The 6 advanced systems:
- RF Scanners
- Pick to Voice
- ASRS
- Pick to Light
- Advanced Labeling Techniques and Solutions
- RFID
RF Scanners
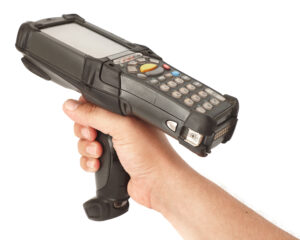
Hand holding bar code scanner.
Radio Frequency (RF) scanners have been in use for several decades. The RF device is a small handheld computer that is usually shaped in the form of a pistol. These devices typically log into a telnet style session. The user then navigates through text-based screens to reach a screen that requires that a transaction take place. The user can either manually key in the information or scan a barcode that will populate the same information. Ideally, the scan would be faster than the manual input.
Recently, updates to the user interface have been made. These updates utilize a GUI based interface. These can look like Windows or a more user-friendly smartphone-style interface. Regardless of the interface, the navigation and processes to perform the required tasks remain the same.
Perceived Advantage
Many WMS Solutions will require this system as the base level of entry. You have a worker on the floor performing the same transactions that a data entry clerk would do while they are
performing the physical move. This leads to the following benefits:
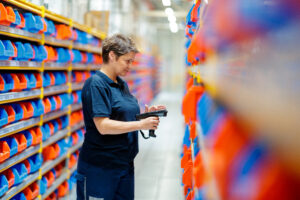
Warehouse worker scanning the barcode on a box in a warehouse
- Near Real-time Inventory data (data lag-time is dependent on the worker completing the transaction and the system processing the transaction promptly)
- Higher Inventory accuracy – fewer errors due to misreading/typing information
- Reduction in resource overhead (Elimination of the data entry worker)
Barriers to achieving the desired result
Many warehouses that are looking to implement RF scanning technology currently have a workforce that is very physical in nature. A forklift driver simply moves material. Movements within a warehouse are not tracked. These transactions are extra work. The extra work is perceived as a non-value-add task.
An RF device adds time to their task by requiring them to input information into the device and read the instructions being dictated by it. Add in the additional 1-2min to login and navigate to the task screen and they are already on edge. In bright outside environments, some RF devices may experience issues as the laser may not bounce back to the device and the barcode may not be properly scanned. These conditions can render the RF devices’ barcode scanner inoperable and the user will need to manually key in all the required information.
System connectivity and network signal strength are also key factors to using RF. If you can’t connect to the system, processes can come to a halt and the warehouse is no longer productive.
Pick to Voice
Pick to Voice devices have been in use for some time, but not as long as RF devices. Like RF, it is a small handheld computer that requires the user to log into a telnet style session and the user navigates through text-based screens to reach a screen that requires that an inventory transaction take place. However, instead of performing an RF scan or manually inputting information, the user is talking into a microphone. These tasks are executed using a headset. The headset is used to relay and confirm the tasks. This frees the workers to use their hands and eyes while performing the directed tasks. The interface is similar to someone using Alexa, Cortana, or Google.
Perceived Advantage
Like RF devices, the process behind this technology is that instead of having a data entry clerk log all of the inventory moves from an office desktop computer, you have a worker on the floor perform the same transaction while they are performing the physical move. This can lead to the following benefits:
- Near Real-time Inventory data (data lag-time is dependent on the worker completing the transaction and the system processing the transaction promptly)
- Higher Inventory accuracy – fewer errors due to misreading information
- Reduction in resource overhead – The transactions in the system are performed by the same person who is physically moving the material. This eliminates an additional worker to perform data entry.
- Paperless Picking – The use of a Pick Slip would be redundant and inefficient. The headset doesn’t require it.
Time studies have shown that Pick to Voice systems have faster cycle times for picking and counting (average estimates can range between 1.5 to 3x). This is because the voice of the worker can be relayed over the headset while the worker is visually looking at the item(s) whereas the idle time for the RF barcode to scan and process the information is longer than voice recognition. Language packs are available to make it easier for workers to use their native language. This also helps with multi-lingual international operations. Examples and case studies can be seen on YouTube by searching “Voice vs. RF Picking.”
Voice apps are still an evolving landscape as Perficient’s Eric Enge and Tristan Smith discuss in their video Voice Apps Can Drive Your Business.
Barriers to achieving the desired result
Pick to Voice is an ideal solution for an indoor facility with minimal noise. Wind and other loud noises may cause the device to not work properly. This can cause misinterpretation. Also, another person could speak a command and it could be processed. Because of this, many may choose not to go with this solution. Those who have already invested in RF may see the ROI as too low a number to justify the technology change.
Concerns over validation and quality checks can surface as well. The pick may not be as accurate as of that of a barcode scan because the worker is vocally answering the commands. Using RF or RFID, the system is performing the validation on the physical item itself (ex. RFID chip or Barcoded label). Internal theft or incorrect item selection is possible. Undisciplined employee performance or a misreading of the product can cause this. Depending on the Item nomenclature and warehouse layout, this may not be a common issue.
Automated Storage and Retrieval Systems (ASRS)
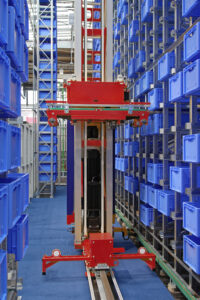
Robotic Warehouse Plastic Crates Storage Retrieval System

Automated High Bay Retrieval System in Warehouse
ASRS is a computerized storage and retrieval system. Bins are used for item storage. These bins are placed into a high capacity storage grid (width and/or depth). A computerized controlled assistant (ex. Robotic arm, conveyor) will store the contents of the bin in a suitable location and retrieve it upon demand.
Perceived Advantage
ASRS Storage areas are designed to be able to store more materials and goods because the need for aisleway/human access is not needed. This results in overall cost savings due to the following:
- Able to Store more materials in a confined space.
- Less time spent hunting for Items. The system efficiently retrieves them from the known location.
- Since the storage and removal are automated, the goods cannot be easily removed without using the ASRS.
- This will increase inventory accuracy and reduce the time spent on Inventory audits.
- Less excess of parts on hand is needed because there is less shrinkage
- Automation reduces the need for manual labor and reduces workforce requirements. Reduction in workforce safety hazards.
- Can be used to seamlessly automate and process orders and pack the goods into a container to be delivered to the shipping dock. Increasing cycle times and reducing the need for manual labor.
- Better warehouse modeling. Using the data and analytics from storage, retrieval, and staging of goods. Once implemented, it will increase the throughput of goods through the warehouse.
Barriers to achieving the desired result
There are four major reasons why an ASRS may not be implemented in a Warehouse:
- Warehouse Configuration (how and where is the ASRS going to be installed?)
- Cost (Hardware, software, training, and support)
- Process Organization (how to go from the current processes and configuration to the new processes and configuration)
- Change Management (How to prepare the workforce and implement the necessary changes to make the new system work)
Pick to Light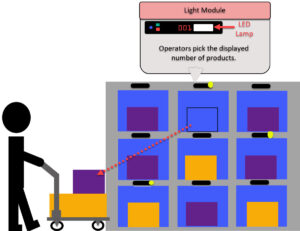
Like Pick to Voice, a Pick to Light system is designed to expedite the picking process in a high-volume warehouse with multiple forward picking locations. Instead of being fed instructions via an RF device or a headset. Lit diodes located on the racks instruct the picker to pick the required goods. Usually, it’s a Red/Green system (Green = pick, Red = Do not pick). The picker will stop at each pick location, take an item out of that location until the lighted diode changes color. (recorded by the user pressing a button near the lighted diode) Once all picks are complete; the worker packs/closes the box. Attaches the final label to the box. They then drop the box off in the staging area.
Perceived Advantage
Instead of reading a screen or scanning barcodes, the worker is looking for a “Green” light. Once found, they press a button to confirm that the pick is complete. Since colors and button pressing are universal uniform actions, there is no added expenditure on having to install additional language packs or requiring a sufficient level of literacy within the workforce. The need to use and maintain RF devices is reduced.
Barriers to achieving the desired result
Additional costs will be needed to set-up the hardware, maintain the diodes, and ensure that the interface between the Pick to Light system and the ERP are working as designed. There is no process in place to perform the “Drop” transaction with Pick to Light as the transactions take place at the point of picking. There is no formal process in place to record the “drop” of the package into the shipping area. This transaction would either have to be assumed to have occurred or recorded via another system (ex. RFID, RF Device). Multiple pickers picking multiple orders and items may not be best suited for this process unless there was another system in place to organize and segregate the bulk picked orders into their intended individual orders once they arrive at the shipping area.
Labeling Solutions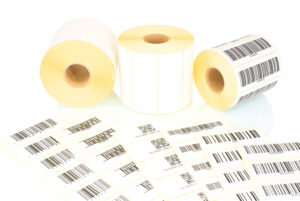
Labeling is key for identifying materials and guaranteeing that controls are in place. A label simply identifies the item/product sitting on a shelf or on a warehouse/manufacturing floor. The identification of these items is key for several reasons:
- Inventory Accuracy: Proper labeling of the material increases accuracy on quantities on hand and demand fulfillment needs
- Government Regulation: There are mandates from local, federal, or international governing bodies mandating specific labeling needs. One such requirement is material composition. An example of this would be the identification of Hazardous Materials. Certain icons must appear on a Hazmat label to stipulate the toxicity, flammability, and special handling of the item. This label clarifies how you properly transport these materials.
- Expedited Picking: Key identifiers on the label and barcodes streamline the process.
How to Obtain Labels
Companies can choose to create their labels internally or outsource them through a 3rd party vendor. The outsourced labels may be a set of pre-produced barcoded number sequences. These sequences have no value until linked with a specific item (ex. LPN, Lot, or Serialized Numbers). They can also have specific identifiers that arrive just as the specified item is ready to receive the label. Labeling is an intricate part of identifying items. Labels ensure the accuracy and efficiency of the execution of a supply chain system. Although the technology is not the same way as that of an RF scanner or a forklift; its importance is just as significant and can hinder the operation of any company if not properly implemented.
Labeling solutions and governance are so important that several companies exist only to manage this. These solutions are so robust that you can have one label template with 12 different deviations based on customer or item rules. Many of these label software solutions come with pre-built integrations into your ERP platform.
Perceived Advantage
Labels give the user a quick way to identify an item/product as it resides in inventory. Additional labeling technology may even further enhance the process and further expedite the transaction. Examples of these are as follows:
- Simple Barcode: A simple 2D barcode when used by a barcode reader can speed up the picking process because it will require that the picker scans the barcode instead of manually entering the item number into the mobile device. The scanning of an incorrect item will lead to the RF device informing the picker of the mistake.
- 3D/QR Barcode: Additional information is embedded in the barcode. This is beyond that of a simple alphanumeric sequence. Document attachments and website URLs are examples of additional information. This is in addition to item identification. A QR Code can have information like a packing slip embedded in it. This reduction results in faster loading and shipping cycle times.
- Data-Field Identifiers (DFI): Alphanumeric characters added to a barcode. They indicate where the information belongs. These limit where the scanned information goes when entered.
- RFID (Active and Passive): RFID labels are more advanced than the QR Barcode. Passive RFID labels require an active transmission from an external source. Active RFID tags continually broadcast their location to an input server (local, Wi-Fi, wireless, cellular, etc.). For more information on RFID, please see the RFID Section.
DFI (Continued)
DFIs tell the inventory system that the code belongs to a specific type of data. For example, a barcode for an item’s location could have a DFI of “+”. A scan value “+A1234” translates to item location A1234. The system would strip the “+” from the data and know that the value only belongs in an Item location field. No other field would get that information. Fewer scans streamline processes. They also increase the transaction accuracy because they restrict the data input and reduce a user scanning the wrong barcode when performing the transaction (ex. Item Number scanned as the LPN number). Additional examples of such identifiers are as follows:
-
- Warehouse Location
- License Plate Number (LPN)
- Item
- Manufacturer Part Number
- Lot
- Serial Number
- Unit Quantity
Barriers to achieving the desired result
Issues that pertain to labeling stem from the following decisions:
- In-house label creation or Outsource?
- Custom Labeling Paper or Generic label stock?
- Home-grown, Generic, or Sophisticated Labeling Solution Software?
- What events will trigger the creation of a Label?
- Are there Customer-specific or Site-specific Labeling requirements that drive deviations from a Global Company Standard?
- How many different labels/label types must there be on any given item?
The ability to properly answer, manage, and govern these processes will result from these questions. An entire business division may need to govern these needs and to monitor the processes and changes. The biggest barrier to achieving a proper labeling solution is the amount of money and time a company is willing to invest in it.
RFID
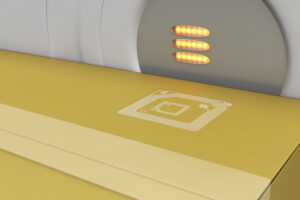
RFID-labeled inbox and antenna
Radio Frequency Identification Devices (RFID) are more advanced technology for Inventory tracking. These are labels with computer chips and a radio antenna embedded in them. RFID Tags are either “Active” or “Passive”. Active tags always broadcast a signal. Passive tags only broadcast when actively triggered.
Perceived Advantage
When properly configured, material transactions are simple and easy to perform. It’s automatic. There’s no need to scan the material. Thresholds are set up to detect when an item has been moved. A transaction signal is sent to the system when an RFID tag crosses a threshold. If “no” thresholds exist, you can scan the RFID tag with a special device. These transactions add a minimal amount of time to the physical acts of performing the physical move. In fact, the idea behind these devices is to allow the worker to concentrate only on the physical movement and let the technology perform all the transactions within the system.
Innovative technology can utilize RFID to perform inventory counting and identification transactions. An example would be a construction company using a mobile flying drone to fly over a construction yard to perform inventory cycle counts. When the drone flies over the surrounding area, it can locate missing items. This is beneficial when inventory is unintentionally moved (ex. Flood, Tornado, or Hurricane).
Barriers to achieving the desired result
Cost is the key barrier to entry for RFID. Active RFID tags cost between 50 cents and $5 a label and passive tags are no down to around five cents a label. Traditional Non-RFID labels cost roughly 0.005 cents per label. This makes RFID thousand times more expensive than a traditional label. Also, the cost of setting up the infrastructure for RFID can be very comprehensive and costly. You will need to configure/deploy additional devices. This is to properly read and pinpoint the location of the material. If network readers are not properly set-up and configured, “GPS drifting” could take place. An item could physically be ways away from the location that the system believes that it is residing in.
Conclusion
Mastering your warehouse and positioning it for continued growth is an ideal strategy to increase productivity and reduce costs. Review these six technologies and figure out which ones are ideal for your business and structure. Not all systems will be ideal. Pick the one best suited for you.