Cycle Counting is a key part of effective controls to maintain the accuracy and overall cost of Inventory. Physical Inventory Counts are critical to managing inventory accuracy and reporting on shrinkage. Effective Cycle Counting can eliminate or greatly reduce the need for Physical Inventory counting. Inventory accountants need to confidently and accurately report these numbers to investors and banks. To perform an accurate full physical inventory count, you have to shut down all operations and count every item in the warehouse. Depending on the size and volume of the warehouse, this process could take anywhere from days to a week. Most companies can not afford such shutdowns for their operations. An alternative to a Physical Inventory count is to perform Cycle Counts instead.
Cycle Counting is a systematic break-up of a warehouse to manageable chunks. These chunks can be a range of items and/or locations. Each “chunk” is then counted on a daily/weekly/monthly basis. Over the course of a fiscal quarter or calendar year, you end up touching every item/location once. Using cycle counts will allow you to concentrate on managing critical items/areas.
Item or Location-based Cycle Counting?
How do you want to Cycle count? Do you want to do it based on location or based on the item? Each process has its merits, but one may be better geared for your warehouse.
Location-Based Counting
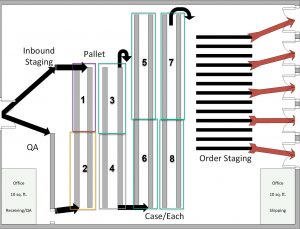
Illustration of location-based Cycle Counting
The traditional thought about cycle counting is that you are dividing the warehouse up into sections and performing a mini-inventory count for each section daily. By the end of a month or quarter, they have touched every location in the warehouse once. Location-based cycle counting is the term for this model of counting. The emphasis is to make sure every location within a warehouse is touched on a regular interval.
This requires a level of organization within that inventory location. If an item has been moved or is missing, you might not discover this during a location-based cycle count. If the item has been moved to a location that is outside of the range of locations, it won’t be found until a later day. The question is whether the touching of every location or the on-hand accuracy is the key metric that you are trying to control with inventory on-hand counting.
Item Based Counting
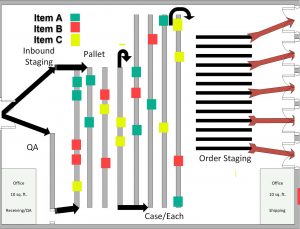
Illustration of Item-based Cycle Counting
Item-based counting is more hyper-focused as it is looking for confirmation of inventory on-hand by item and not just by location. Item-based counting will send a warehouse worker to every location that the system has registered that the item is residing in. Accuracy for inventory adjustments is higher because you are counting the item quantity in totality and not simply for where it resides.
Using item-based counting will allow you to divide up your items into groups and count the groups based on priority (ex. Dollar-value, high-mover, etc.). You only have to count an item twice a year if it is in a group of slow-moving items. The time spent on inventory is reallocated to ensure items with higher demand have a higher level of accuracy.
As with location-based counting. Item-based counting does not take into consideration any item moves that were not registered in the system. If the Warehouse Worker notices that the item resides in two locations next to each other and the system doesn’t ask them to count the item in the second location; that material may not be properly identified and included as part of the counted inventory on-hand. The system may have that material residing elsewhere in the warehouse. The warehouse worker can ignore and solely follow the prescribed tasks. They can take note of the discrepancy and seek advice from their supervisor. Or, they can proactively perform an additional count. This will depend on the policies and procedures of the warehouse.
Hybrid Approach Cycle Counting
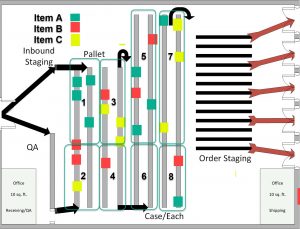
Illustration of Hybrid Cycle Counting
A hybrid approach of using both styles may be the optimal approach for maximizing results. This way you can catch items that have moved with a location-based count and keep tabs on your high-demand items with an item-based count. This way you can incorporate the best of both methodologies.
The downside of this approach is that there will be an increase in management, oversight, and administration. The daily cycle counts task volume will double. Efforts to review and approve inventory adjustments will also be doubled. Counting some locations will occur twice within one day every so often. This is because of an overlap of the two types of cycle counts. If personnel and administrator time utilization is not an issue; I would highly recommend this approach.
Understanding how you want to approach counting and controlling how you want to count items within your warehouse is a key first step in inventory controls. The next step will be how you want your workers to perform their counts.
Scheduled & Opportunistic Counting – How to understand the difference